Concrete Shed Base Cost
- The average concrete base for a shed costs around £100 per m³ in the UK.
- It takes approximately 2 to 3 days to complete this type of job.
- A breakdown of how much different grades of concrete shed base cost per m³ to get constructed in 2025.
- What impacts the concrete base price you're quoted by tradespeople, as well as what's involved in building a concrete base for a shed.
- How to find and hire a builder near you to construct a concrete shed base.
Want to know how much a concrete shed base costs in the UK?
In this guide, we cover everything you need to know about getting a concrete shed base constructed. This includes typical concrete base prices you're quoted in 2025, building regulations you need to know about, and much more!
Ready to get a quote for a concrete shed base?
Get free, no obligation quotes from local builders who can handle all of this for you. MyJobQuote is fast, easy, and connects you with professionals in your area.
Want to find out more before you start getting quotes?
Continue reading below!
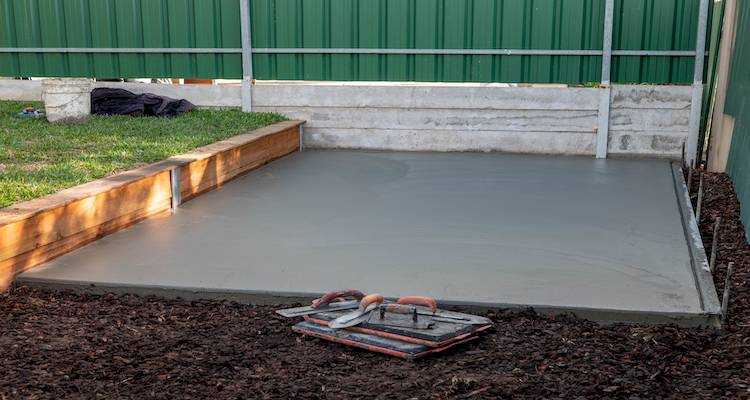
£100 per m3
Table of Contents
- How Much Does a Concrete Shed Base Cost?
- What Is the Cost of Concrete Base Materials?
- How Much Does Shed Base Installation Cost?
- What Impacts Concrete Shed Base Costs?
- Additional Costs of Concrete Base for a Shed
- What's Involved in Installing a Concrete Shed Base?
- Can I Install a Concrete Shed Base Myself?
- Building Regulations & Planning Permission for Installing a Concrete Shed Base
- Types of Concrete Shed Base
- Hiring Contractors for Installing a Concrete Shed Base Checklist
- FAQs
- Sources
How Much Does a Concrete Shed Base Cost?
Getting the foundation right is a critical element of installing a new shed in your garden.
If this isn't done right, then your shed installation might develop a number of issues. This could include water damage and rot, as well as subsidence if the base can't support the weight of the shed.
The bottom line is this:
If you want to keep your shed for a long time, then you must get the foundation right. And the most popular option used by UK homeowners who want the most durable and long-lasting is a concrete shed base.
Despite their simplicity of design, concrete bases come out ahead of the competition in many ways.
We'll get to this later in this guide — but let's first deal with what you should expect the cost of a concrete shed base to be in 2025.
How much a concrete base for a shed costs depends on the type of concrete you're looking to use and how deep the concrete shed base needs to be.
Poured concrete usually costs between £75 and £95 per m³. For a small shed, the concrete alone will cost around £40.
Concrete pouring costs around £90 to £100 per m³ for grades C8/C10/C15. Expect to spend around £100 - £110 per m³ for grades C20/C25.
The average price for C30/C35 grades is £110 to £120 per m³. If you need grades C40/C45 concrete, the average cost of pouring concrete is about £130 to £140 per m³.
Pouring concrete is also typically priced per cubic metre (m³) because you need to fill a volume (i.e., length by width by depth) rather than an area (i.e., length by width).
Unsure how much concrete you'll need for your shed's foundations?
The best thing you can do is consult with a builder near you who understands what's required to correctly lay a concrete base for a shed.
There's no cost, no obligation, and no hassle when getting quotes from tradespeople near you via MyJobQuote.
Concrete Shed Base Prices
Size of Shed | Concrete Type | Cost |
---|---|---|
4m x 6m | Pouring concrete | £300 - £350 |
6m x 8m | Pouring concrete | £450 - £500 |
8m x 10m | Pouring concrete | £550 - £600 |
4m x 6m | Concrete slabs | £300 - £350 |
6m x 8m | Concrete slabs | £450 - £500 |
8m x 10m | Concrete slabs | £550 - £600 |
Several factors may influence the final cost of constructing a concrete shed foundation.
For example: If you plan to have orders and pour concrete, easy site access is critical. Your quote will also be higher for installing a concrete slab if you transfer the concrete with a wheelbarrow.
If you use concrete slabs, you can normally get them for free or low cost. The tradesperson who arrives to place your concrete slab may include turf or soil removal in their quote.
If they do not, inquire with your neighbours, co-workers, family, and friends. Also, check with the local recycling facility or tip before hiring someone to remove the turf as well as the soil.
What Is the Cost of Concrete Base Materials?
A shed base necessitates only four substances: type 1 MOT, sand, cement, and some wood, though edging boards or other simple and inexpensive materials will suffice.
We'll only go over supply costs for a concrete shed base in this section, so you know what you're in for if you decide you want to do this job yourself.
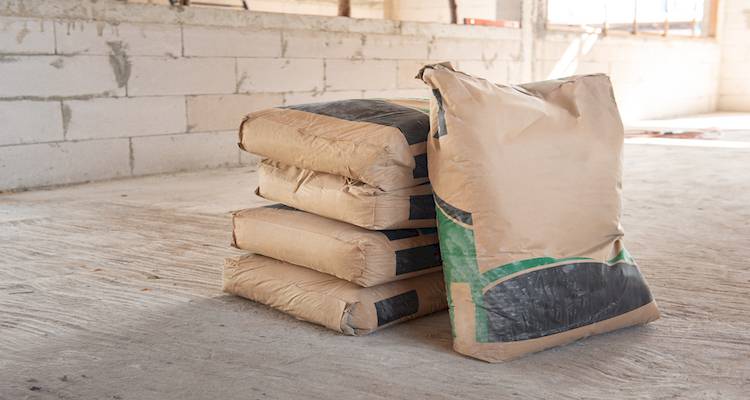
Most people buy edging boards from Wickes since they appear to be the best deal, with a pack of 5'8 foot cutting boards costing between £25 and £30. When all the sides of a 6 x 8-foot shed are added together, the total length is 28 feet.
You must spend no more than £45 on wood when building the wooden board for your concrete shed base.
It is strongly recommended that you use type 1 MOT since it compacts the ground once it has been tampered with, decreasing the possibility of the ground shifting or breaking your concrete slab in the future.
You should use 2 inches (50mm) of type 1 thread. One bulk bag of type 1 MOT must cover eight sqm at a depth of 50mm, suggesting that one bulk bag would be sufficient and that smaller bags might be worth considering. Although more expensive than purchasing in bulk, this method will save you time and money when discharging any leftover hardcore.
You can pay £50 per bag. Remember to not have type 1 MOT at the border edges because once the concrete is set and the boards are removed. When building a concrete shed base, ballast is the right type of sand to use. The most budget-friendly way is to buy this sand is in bulk bags.
A bulk bag of ballast usually covers a large area. The best depth for a concrete foundation is 75 – 100mm, which means one bulk bag of ballast should suffice. It is recommended that 4 - 5 bags of cement be bought for each bulk bag purchased. A ballast bag should not exceed £50, and a bag of cement must not exceed £5.00 (£25 for five bags of cement). Therefore, the overall cost of the cement and sand is £75.
How Much Does Shed Base Installation Cost?
So, how much is it to lay a concrete base in the UK?
Concrete bases can be challenging to install. Concrete is the more labour-intensive of the two options, and if installed inaccurately, it can be expensive and physically demanding to remove.
The labour costs for attempting to install a concrete shed foundation range from £40 to £50 per m². This varies based on the complexity of the job and the time required to pour the concrete. For labour, you should budget around £220 and £450 per day.
Make your choice determined by the type or size of shed you wish to build. Your decision is influenced by what you aim to store in it, the demands of the location, and your budget. A small shed's requirements differ from those of a large shed. The open bottom or constructed floor, and the sloped or flat ground, influence your decision.
Based on the installer's knowledge and prep workload before laying the material, concrete bases could take somewhere between 24 to 36 hours to lay and begin to set.
What would you suggest to lay a shed floor on? Can you also allow for a soakaway to stop any ingress of water into the new shed (currently happening)?
Most concrete bases necessitate the addition of a border to prevent the concrete from spilling out, which is done after the ground is prepared and before the concrete is laid. It takes roughly seven days for the concrete to heal and be ready for a shed or garden building after levelling the base.
Most installers advise using support structures throughout your concrete base, which increases the amount of work. PSB does not necessitate the use of any support structures. Concrete is a labour-intensive material that, if installed by hand, can take several hours to lay and level correctly. If done incorrectly, it can be costly and permanent to replace.
PSB can sit on top of a sub-base and protrude without requiring a border and still work well. Concrete needs a solid border to prevent it from spilling out of its place. PSB can bulge and sit on top of a sub-base without a border, but it still works well.
What Impacts Concrete Shed Base Costs?
There are many reasons why the price of installing a concrete shed base varies. In this section, we go over the different cost factors and how they affect the overall cost.
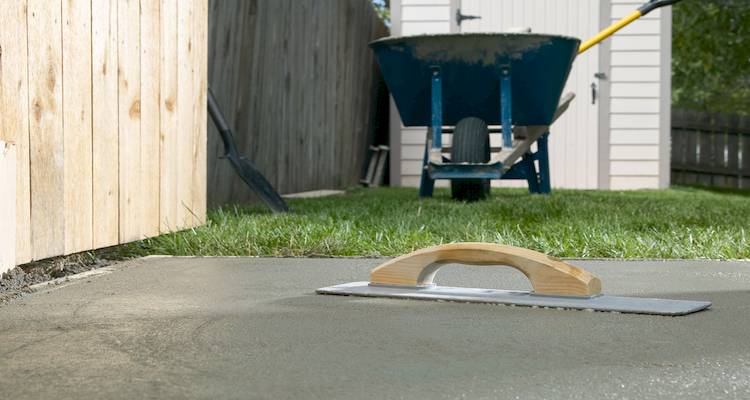
Location
Because tradespeople's prices vary across the country, the cost of installing a concrete shed base will vary depending on where you live.
Hiring costs in the southeast, on the other hand, are typically greater than the average, particularly in London. However, costs are generally lower in northern England, Scotland, or Northern Ireland than in the rest of the nation.
Amount of Tradespeople
The cost of erecting a concrete shed base is also determined by the number of tradespeople required, influenced by the size and type of concrete base required. The greater the number of tradespeople required, the more costly the installation.
Size
It should be no surprise that the larger the shed base, the more expensive the repair. A bigger shed base will have greater labour or supply costs than a smaller one.
Duration
The higher the labour cost, the longer it takes to install the concrete shed base. However, the longer the hiring time frame, the more you will pay, with some property owners having to employ repairers for a few days while others must hire them for several weeks or months.
Materials
Most people envision a garden shed as a wooden structure with a bitumen felt-covered roof. However, an old, corrugated iron or concrete shed will frequently suffice.
Except for permanent outbuildings, these are rarely used these days. Garden sheds made of aluminium or plastic, on the other hand, have recently grown in popularity.
Although wooden sheds are wonderful, a metal shed is far more secure and comes in various colours thanks to hot-dipped plastic coatings. On the other hand, a metal shed is often more expensive than a wooden shed but requires less maintenance over time.
Doors
Depending on the purpose and style of your shed, you can choose between single or double doors. Some people use big sheds instead of garages, which require double doors. Because of the extra work involved in manufacturing, sheds with two doors are much more expensive than those with one.
Windows
If the shed is only used for storage, the window is unnecessary and reduces the shed's security and privacy. However, if it is a workshop or office, natural light from a window is required.
However, for the summer months, purchase one with opening windows and secure window fastenings.
Additional Costs of Concrete Base for a Shed
You could decide to have additional work done when installing a concrete shed base to give your garden a fresh look! Or, in some cases, minor details can add up to a high cost. As a result, we'll cover the extra costs of placing a concrete shed base here so you know what to expect.
Patio Installation Cost
The typical income of laying a patio in a 20 sq m area ranges between £900 and £2,500. This price includes the cost of excavating the area, laying the foundations, purchasing, and laying the patio slabs.
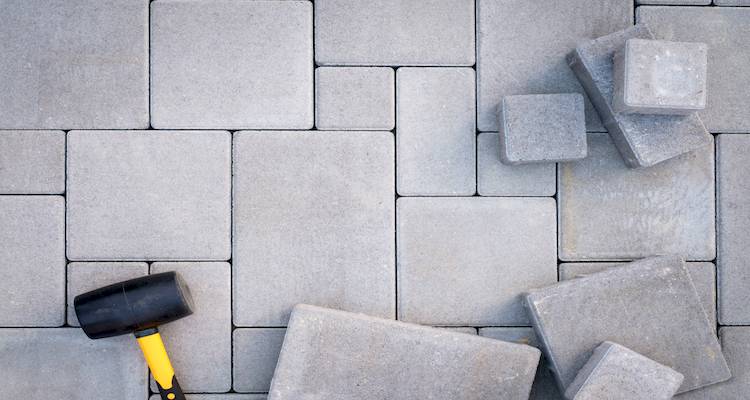
Prices will vary based on the supplies used; for example, budget options like concrete and brick patio slabs start at £15 per square metre, whereas premium patios are typically made of slate, which varies from £900 to £3,800 for installation, and a stone patio can cost up to £4,600.
If you would like further information, please refer to our guide on the costs of patio design and installation.
Landscaping Cost
If you wanted to hire a gardener to lay turf, the average cost would be £260 to £300 for a 20m² area and £650 to £750 for a 50m² area. Artificial grass costs around £1300 to £1600 for a 20m² area and up to £3,250 to £4,000 for a 50m² area.
Decking would cost around £600 to £750 for a six-metre square area or £1000 to £1250 for a ten-square-metre area. If you want a raised vegetable bed built, consider paying £120 to £520 for a 4m² area.
When it comes to creating a patio, the cost is around £360 to £480 for a 4m² area or £800 to £1200 for a 10m² area. A one-square-metre pond in the back garden will cost between £260 and £530. The landscaping cost can be determined by the size of the garden, easy accessibility, and where you live.
Property location is important because landscapers, like construction companies in general, charge different rates in different country regions.
If you would like further information, please refer to our guide on the costs of landscaping.
New Garage Cost
A garage can cost anywhere between £4,200 and £20,000 to build. This includes the cost of materials and the hiring of a builder to complete the work. The type of garage, the work quality, and the size of the installation can all impact the final cost.
Naturally, the higher the costs, the larger the garage. Similarly, your costs will rise if you want a high-quality finish or a costly garage door.
New Garden Shed Cost
Garden sheds are specifically designed to help you store and organise your gardening needs.
Without a garden shed, you'll be required to leave garden tools and materials out in the open throughout the garden, making them difficult to find, vulnerable to water damage, and easily stolen by burglars!
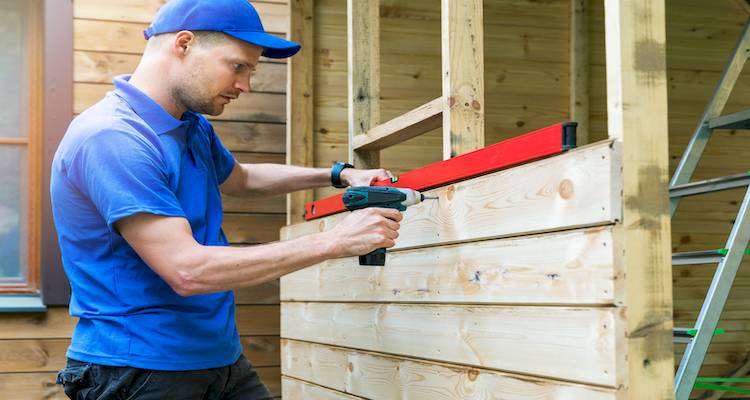
Instead, everything can be kept neat and dry in a garden shed, right where you need it. Installing them typically costs between £500 and £1,000.
What's the average cost to get a shed fitted? I already have the shed materials.
What's Involved in Installing a Concrete Shed Base?
A great shed is also a beautiful natural wood addition to your outdoor area. It is worth the effort to build a shed that's both attractive and sturdy, as well as functional — and that has to begin with the foundations.
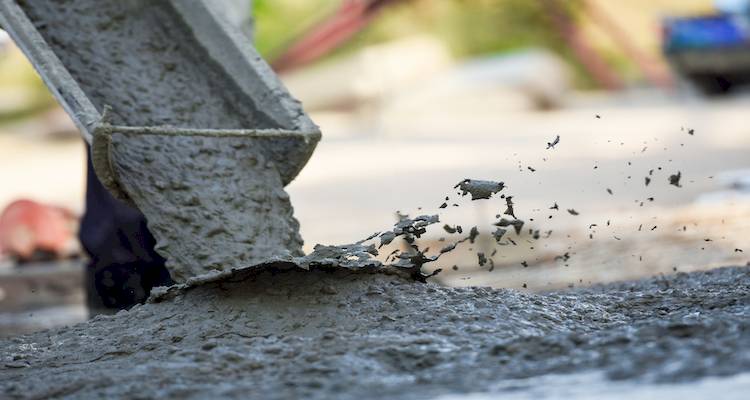
Without a firm and level foundation, your new outbuilding may appear new, but it will quickly become unusable.
You can rent all the tools and equipment you'll need to lay a concrete foundation for your shed, and we'll walk you through the process so you can decide whether to do it yourself! So if you’re wondering how to build a concrete shed base, read on…
Step 1: Measure and Make a Mark
Begin by marking out the region for the slab once you've decided on a location. Make it bigger than the shed and leave enough room for the formwork — the wooden frame that will go around the area's perimeter to keep the concrete in position.
Next, push a wooden peg into the surface at each corner and connect them with a taut length of the string. Finally, measure both diagonals to ensure the corners are square. You must adjust if they are not the same.
Step 2: Excavate the Foundation
A 100mm sub-base, as well as a damp-proof membrane, will be installed beneath the slab. As a result, you must excavate a level-bottomed pit 100mm deep. Eliminate all grass or other vegetation, stones, and debris before compacting the earth. A micro excavator would then make quick work of the excavation.
Step 3: Install the Sub-Base
Because you can't lay a concrete foundation directly on soft ground, a hardcore sub-base is required. The best material to use is MOT Type 1 hardcore.
When your gravel sub-base is in place, compact it thoroughly with an HSS light vibratory wacker plate. Next, spread a sand layer on top to protect the damp-proof membrane from the sub-base stones.
Step 4: Shed Gravel Foundation
Using 150mm x 25mm extents of treated timber, build a frame the size of the slab you're making. Make certain that the frame is square and level with all sides; otherwise, your shed will be off-kilter.
Place the frame where the base will be. Now, at one-metre intervals, drive wooden posts into the surface around the formwork. This will prevent the planks from bowing underneath the weight of the concrete. Using a spirit level, ensure that the formwork and posts are levels across all sides.
Step 5: Install the Damp-Proof Membrane (DPM)
Covering the full sub-base with heavy-duty plastic sheeting, the edges turned up within the formwork to form a tray. If there are any joints, ensure that they are overlapped and taped. This DPM serves two functions:
- It keeps the concrete from drying out too fast, which could lead to cracking.
- Reduces condensation issues in your shed.
Step 6: Purchase the Concrete and the Mixer
Multiply the slab's length, breadth, and depth to get the overall amount of concrete needed.
Order your concrete, then hire a concrete mixer. A typical concrete mix for shed base ratios is one part cement to five parts aggregate and sand. If you have any doubts about the quantities, consult your concrete supplier.
Step 7: Prepare the Concrete by Mixing, Pouring, and Spreading It
Cement is corrosive and can cause severe skin and eye damage. As a result, your top priority should be to work safely. Once you're ready to begin, time is of the essence because concrete begins to degrade around two hours after it's been mixed. A wheelbarrow can transport concrete from the mixture to the site for a slab the size of a typical garden shed.
Keep in mind that collaborating with concrete requires two people to keep everything moving.
Because the fresh concrete is moist, it spreads easily with a shovel or rake. When all the concrete is in place, level it with a straight-edged wooden piece and tamp it down. Tamp again to create an even surface and remove any air bubbles. Finally, spread a raised polythene layer over the concrete to prevent it from drying too quickly, which is how cracks appear.
Step 8: Allow Time for the Concrete To Cure
It will take at least 48 hours for your concrete shed slab to be dry enough to step on, but it is preferable to leave it for longer. Once the formwork timber has dried, you can remove it since it will take 28 days to cure but be ready to bear weight.
Can I Install a Concrete Shed Base Myself?
If you're constructing a shed or another structure in your garden, including a greenhouse, summer house, or even an office, you'll need to provide it with a sturdy and strong concrete foundation that will support the framework, provide a level base, and protect it from rot caused by groundwater seepage.
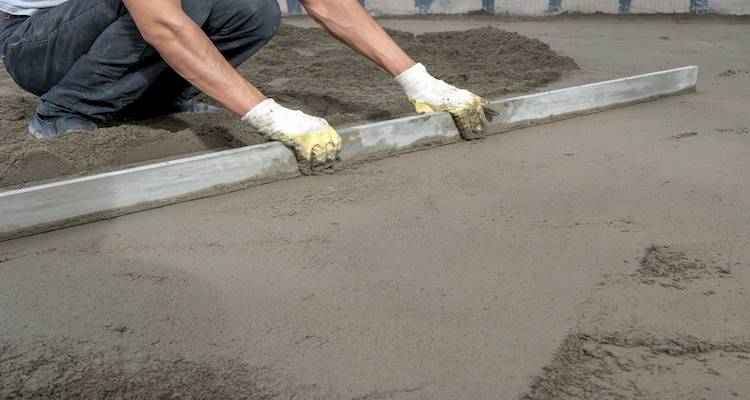
If you're used to doing your own DIY projects, you can simply build your own concrete shed base in a day or two. However, you must understand what could go wrong to avoid these minor errors. Here, we will go over what you need to have and be aware of.
It's critical to double-check your preferred shed location in relation to your property lines. In addition, most towns and villages have a particular criterion for building setbacks, which you should check before beginning construction.
I need a base for a garden shed, but what's the cheapest and best way to lay a base down? The shed is 8ft x 6ft, and I want to lower costs by laying the base myself.
If you level the frame, making sure that you leave it at a slight fall so the water will run off, it’s then just a matter of filling with a concrete mix of ballast and cement being sure to pack it into the corners, you can use a concrete float to create a smooth surface, or the backside of a landscaping rake to create a non-slip surface.
So long as the frame is filled to the top, you will have a level base to place your garden shed in 24 hours or once the concrete mix is set.
This is by far the easiest method I have found to create a cheap level shed base.
A flooded shed is exactly what you don't want! If you choose, you should avoid putting your shed in any swampy or low-lying regions of your property. Instead, find a high, well-drained location and prepare the ground for your shed there.
One of the simplest ways to cause problems with your shed is to simply place it in the garden without first ensuring that your chosen location is level!
If the project appears to be a little larger than you want to take on, you can always hire a professional planned construction contractor to do the ground preparatory work for your shed.
Would putting up a shed, including creating a solid base for it, be within the scope of most handymen?
However, if the shed would stand on the ground, soil or grass it would require wooden or concrete base. This might require a different type of tradesperson."
Building Regulations & Planning Permission for Installing a Concrete Shed Base
When it comes to purchasing a garden shed, summerhouse, or other garden building, it is all too easy to believe that looking at glossy brochures, flashy websites, or, ideally and highly recommended, visiting a garden shed showroom is all there is to it, apart from paying for it, of course. You'll also need a sturdy foundation for your shed if you want it to last if possible.
However, you must consider whether planning permits are required. Regulations and guidelines have evolved over time to reflect changing needs. Consider any available advice and, if in doubt, contact your local council.
The key criteria are that your garden shed is at least 2m away from the boundary IF it is taller than 2.5m. Most sheds are under 2.5m in length, but some are not.
Planning permission is usually required if the property is a flat, maisonette, or used for a business. You will also discover that permission is likely to be necessary if the building's gutters or foundations intrude on your property.
If you intend to live there, you will need both planning permission and building regulations approval. Usage as a business is sometimes permitted if you are not employing anyone there but check with the local planning officer to be sure.
The proposed garden shed, summerhouse or outbuilding may not be built ahead of any wall constituting the front of the original building, and it may not be more than one storey high or higher than four metres with an apex roof or three metres with a pent roof.
It cannot take up more than half of your garden, cannot have a raised decking of more than 30cm, and cannot have a veranda or balcony. In most cases, planning permission may be required, so check with the local planning officer.
Can I build a brick shed DIY? What sort of building regulations/planning permission rules might apply and what can and can’t be undertaken DIY?
The best way to find out for sure is to ring your local council planning team or use their online portal, as each council have different planning requirements.
With regards to doing it DIY what takes you 3 days would probably take a bricklayer 1 day so I would question how much you could earn in your job in 3 days and is it worth the stress?
Bricklaying looks easy but it's not, it takes years to become any good at it."
Planning permission may also be required for your new garden shed if your property is a listed building, is in a conservation area, or is in an area of scenic. Again, your local planning officer will guide you in these cases.
It is possible that a garden shed, summerhouse or other garden building was erected without permission, in which case the planning officer may necessitate retrospective planning permission.
These same residents later claimed that the garden shed would be used to house pigeons, but the local planning committee determined that the garden shed did not violate any regulations or guidelines.
Clearly, planning laws exist to protect the community's interests, which is important; however, common sense should be the watchword, especially when it comes to a garden shed. When you inquire about a planning application for a new shed, the planning officer may grant you a letter of entitlement to give you peace of mind.
Types of Concrete Shed Base
Concrete slabs are among the safest and most secure garden building foundations that can be made or purchased. Concrete slabs can be built to precise dimensions and serve as a highly stable, weather-resistant foundation for any timber, plastic, or metal structure.
In this section, we will discuss the various types of concrete shed bases and their advantages and disadvantages.
Pavers Made of Concrete
A beginner's shed foundation is appropriate for pre-built or home-built sheds. Paver foundations are constructed on levelled exposed ground or sand. They provide a solid flat foundation for constructing or constructing a shed and evenly support the floor.
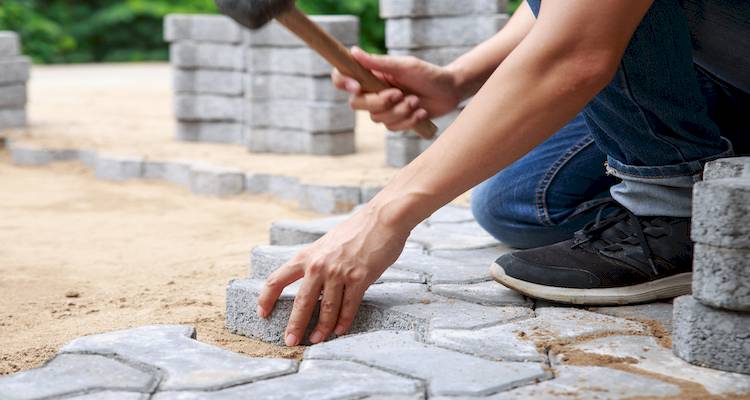
The bigger the paper, the tougher it is, but it requires fewer pavers. Pavers work well on level ground for smaller sheds with or without a floor made of wood, metal, or plastic. Because pavers are used, the entrance is close to or on the ground.
Once the ground has been levelled, pavers are simple to install. However, if the pavers are to be laid on sand, they must first be levelled. This is because sand also assists in levelling the pavers.
They cost £100 and £200. Pavers are priced according to their size, colour, and shape. Large steel mesh pavers are available, and they're more expensive.
Pros
✔ Available in a variety of colours and sizes
✔ Quick and simple to install
Cons
✖ Can settle into the soil over time
✖ It can crack when subjected to heavy loads
Blocks of Solid Concrete
A good foundation for any size shed, ideal for prefabricated or custom-built sheds. Concrete blocks can be rectangular or square.
Only use solid concrete blocks. They must be level with one another and sit on the ground. The number of blocks needed is determined by the shed's dimensions and the ground slope.
You are only levelling the base blocks and not the ground itself. Levelling the blocks and squaring the corners are the most difficult steps. When the terrain is slanted, the difficulty level rises. It is usually in the region of £100.
The size and shape of solid-concrete blocks determine their price. The amount required will be affected by the size of the shed and the slope of the ground. The height of the shed from the ground is another factor to consider.
Pros
✔ Good for small sheds
✔ Easy to stack
Cons
✖ It has the potential to sink over time
✖ Unsuitable for steeper slopes
Timber Frame and Gravel Pad
A simple foundation is suitable for ready-made and home-built sheds of any size. This is more challenging for the inexperienced DIYer due to the size. The gravel pad and timber frame foundation are ideal for flat ground. The most difficult steps in this foundation are aligning the 4"x4"s and squaring the corners. This ranged in price from £200 to £400.
Pros
✔ Easy to level
Cons
✖ High rot risk
Slabs of Concrete
A wonderful foundation for any size shed garage, or even a two-story house, whether ready-made or custom-built. The various steps make this harder for the inexperienced DIYer to complete, and it's a more difficult foundation to construct.
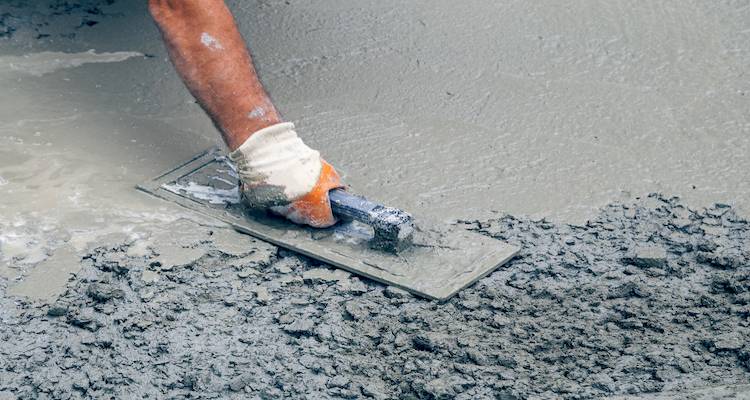
The amount of space required is determined by the size of the shed. The finished slab can support cars and sits on the surface, making it simple to enter.
This costs around £2,500 and £4,000 for a 300 square foot pad. The total cost of all materials will vary depending on the area. Rentals/hires of equipment and Building Code requirements also increase the cost.
Pros
✔ It is permanent and can withstand heavy loads
Cons
✖ Pouring requires temperatures above freezing, and it can crack over time
Hiring Contractors for Installing a Concrete Shed Base Checklist
Request Recommendations
Your friends and neighbours may know someone who has recently finished a project in their home. They may also be able to advise you on who to avoid, which can be equally beneficial.
If you need someone to perform a conversion or extension, make sure they have many experiences. If you own a period asset or live in a Nature Preserve, you want to know that the tradesperson you hire has experience with similar properties and areas.
Request that References be Provided
You should not be afraid to request references from any tradesperson you are considering hiring. If they refuse, you might be best off choosing somebody else.
Look for Them on the Internet
A quick Google can reveal a lot of information. If they have a business Facebook page, see what comments and reviews they've received.
FAQs
How much concrete do I need for a shed base?
What is the easiest base for a shed?
What is the maximum area of a shed without needing planning permission?
Is it cheaper to pour your own concrete?
Do all sheds need a foundation?
Sources
https://www.hss.com/blog/concreting-and-preparation/a-step-by-step-guide-to-laying-a-concrete-shed-base/
https://www.siteprep.com/ground-preparation-for-a-shed/
https://www.leisurebuildings.com/top-buying-tips/do-i-need-planning-permission-for-my-new-garden-shed/
https://www.rias.co.uk/news-and-guides/tips-and-guides/top10-tips-on-how-to-find-a-reputable-tradesman/