Polymer Render Costs
- The average cost of polymer rendering is £30 per m2
- For an average semi-detached house of around 200m2, the total supply cost will be in the region of £6,000
- An overview of polymer rendering and its costs
- Hidden costs, labour charges, and supply costs associated with polymer rendering
- Additional considerations for your polymer rendering project
Polymer render is a modern alternative to traditional renders, incorporating polymer additives like acrylic, silicone, and other synthetic resins for enhanced water- and weather-proofing.
It's ideal for both internal and external walls, offering a modern look without the traditional rendering appearance, such as pebbledash.
We can also connect you with polymer render contractors in your area, which means you can get at least three jobs for the job.

£6,500
Table of Contents
- How Much is Polymer Rendering?
- Supply Costs
- Additional Costs
- Labour Costs and Timescales
- Cost Factors for Polymer Rendering
- Building Regulations Related to Polymer Rendering
- Types of Polymer Rendering Finishes
- Alternative Types of Rendering
- Removing Existing Rendering
- Hiring Contractors Checklist for Polymer Rendering
- FAQs
- Sources
How Much is Polymer Rendering?
Per m2, the average cost of polymer rendering is £30. This means that, for an average semi-detached house of around 200m2, the total supply cost will be in the region of £6,000 - rising to £9,000M for a detached home of around 300m2.
If you opt for a polymer render system, your costs will largely be the same as that of acrylic render, with monocouche - that can rise to £75 per m2 - being more expensive. It’s common to see higher prices in cities where the demand is higher.
Polymer Rendering Prices
Property Type | Service | Estimated Cost | Time Required |
---|---|---|---|
2-bed bungalow (100m2) | Polymer render application | £3,000 | 1 day |
3-bed semi-detached (200m2) | Polymer render application | £6,000 | 1 to 2 days |
4-bed detached (300m2) | Polymer render application | £9,000 | 2 to 3 days |
Supply Costs
Polymer-based render costs around £30 per m2. As it is a specialised job, you’re not advised to undertake it as a DIY project as there is the precision required in how you lay the materials - and doing so incorrectly can not only look bad but have structural repercussions that will require remedying.
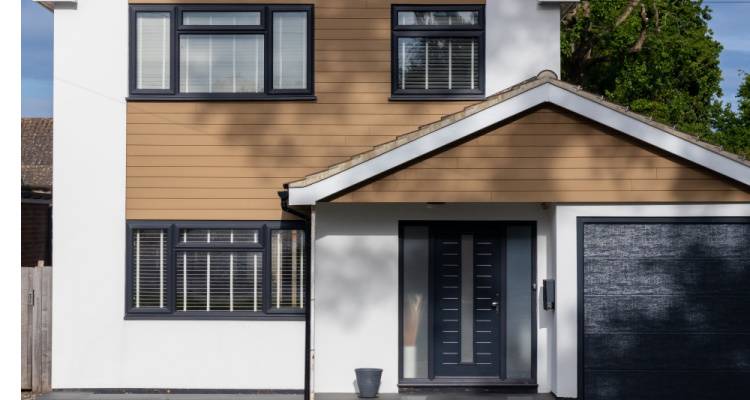
Rather than buying all the necessary supplies yourself, it’s a good idea to speak to your contractor to find out if they would source the items for you. This way, you can take advantage of their trade discount for bulk buying, as opposed to spending more on individual items that you source yourself.
Additional Costs
You will also need to consider any additional costs, as well as the basic polymer render cost. Here, we’ll take a look at some of the fees that might be forgotten but are essential components in your rendering project.
Scaffolding
Scaffolding is likely to cost between £750 to £900 to fit a semi-detached house for painting or plastering access, with the cost rising to £900 to £1,150 for a detached property. This is for a 1-week hire period, and prices can fluctuate based on your location and the period of your hire.
Waste Disposal and Skip Hire
If you are having old rendering removed, you are likely to need a skip present. Mini skips are around £90, while the largest skips can cost closer to £800. Large skips are most suited to rendering projects. A 20-yard skip will cost between £300 to £600, with a 40-yard costing between £400 to £800.

Costs in London are expected to be between £50 to £350 higher than in other locations, due to increased demand. You will need to ensure that your skip is suitable for the type of waste you will be producing, as incorrect labelling can lead to fines.
Permits
You’ll need to check with your local council to see if you need a permit for your skip hire, which can range from £10 to £70, depending on your location. You can face fines of £1,000 if you don’t get a permit before having your skip delivered if you’re storing it on the roadside.
Labour Costs and Timescales
Applying polymer render is a specialised skill and isn’t something you can attempt as a DIY project. Per the rendering specialist, you’re looking at daily costs of between £130 to £250 - the higher the cost, the more experienced the trader is likely to be.
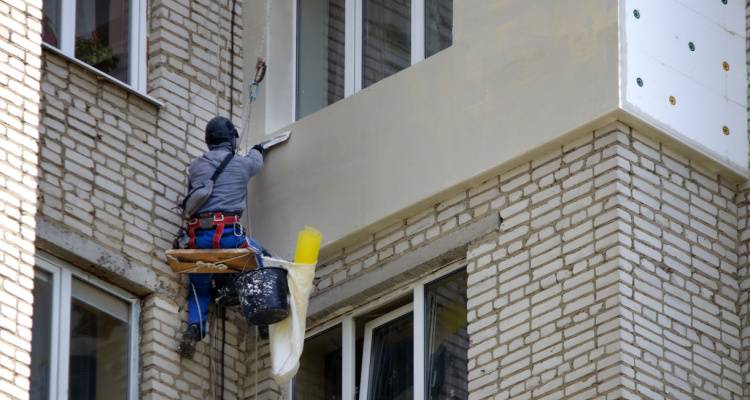
Tradesmen can help to bring down supply costs, however, as they can take advantage of bulk buying opportunities, with the discount being passed on to you. So, instead of buying your supplies one by one, you can get them all at once at a reduced price.
Polymer render is typically quicker to cure than traditional sand or cement render, so you can expect this to be complete within a few days, rather than weeks.
Cost Factors for Polymer Rendering
More factors impact the cost of polymer rendering further to the supply and labour charges - there are a few decisions you can make along the way that can impact your project’s fee, which we’ll look into now.
Location and Ease of Access
Starting with the non-negotiables - location and ease of access. It’s common to see higher charges for labour in cities as opposed to smaller towns due to the increased demand - you’re also likely to face longer wait periods due to this.
If you live in a house without a driveway or a private place to park, you will also need to consider the collection of parking permits. This is also true if you require skip hire - to store it on the road, you’ll need a permit, which can range from £10 to £70 depending on your area, and you can face fines of £1,000 if you store a skip on the road without a valid permit.
Perhaps your property overhangs a public pavement - you may need to have a public right-of-way closure permit from your council to ensure that no health and safety regulations are breached. Your contractor will be able to advise you on the need for this, but generally speaking, if you are working from a height and this obstructs a public footpath, you will need a closure permit to make the working environment safe for your labourer and the general public.
Condition of Substrate
You may have already had your existing render taken off, which can lead to damage to your property’s substrate. Most commonly seen with pebbledash removal due to the harsh nature of the removal process, your contractor will need to repair any problems - costing between £150 to £350 for small patches - before starting work on the new render to ensure your structural integrity and thermal efficiency aren’t compromised.
Complexity of Application Process
If your home spans multiple storeys, you are likely to see a rise in your labour costs as a result of the added labour and potential for more specialised scaffolding equipment.
Opting for a low-effort rendering application is the best way to negate any potential spikes in price, meaning choosing off-the-shelf colours instead of bespoke ones, and smooth textures instead of time-consuming, hand-drawn variations are best for cost-effectiveness.
Building Regulations Related to Polymer Rendering
If you’re applying polymer render to your home’s exterior for the first time or removing an existing external coating to replace it with something new, you will need to ensure that your property’s insulation isn’t compromised in doing so. Your rendering specialist will need to consider both the U-value (thermal transmittance) and the reciprocal R-value (minimum thermal resistance) to calculate the need for additional insulation as a result of the change.
While polymer render application is likely to fall under permitted development, you may still need to have an assessment to confirm the proposed changes. This is because alterations to a property’s exterior can have impacts on fire safety, structural stability, and insulation, all of which fall under building regulations' jurisdiction.

However, if your home is a listed property, you will not be allowed to change its appearance from its original state. This will prevent you from making changes to the external facade, including the colour, texture, and finish.
Those living in conservation areas will also encounter restrictions to ensure the characteristics of a certain geographical area are conserved for historical purposes. This will likely prevent you from making any changes or just minor modifications in the form of maintenance to your existing wall coating.
Whatever your circumstances, you should check with your local planning authority or conservation officer before you start any external rendering project to ensure that you adhere to the guidelines in your area.
Types of Polymer Rendering Finishes
Able to bond to cement, clay, concrete - and more - polymer rendering is a premium exterior wall coating with in-built waterproofing. Further to this, you can choose to personalise your rendering with different types of finishes, as well as colours, to suit your desired aesthetic - but these choices do carry different budgetary requirements.
Opting for a smooth finish will always have the lowest charge when compared to a specialised pattern or decorative finish, and is best suited for those looking for a comparatively cheap option. If budget isn’t an issue, you can choose a decorative finish, such as a pattern or stippled effect to add more personality to your design - but this will add to your contractor’s labour hours, and therefore raise your prices.
Alternative Types of Rendering
To help you choose the right rendering type for you, let’s take a closer look at some alternative types of rendering - including cladding and painting - to give you an idea of what’s available to suit your budget.
Render Over Existing Render
A common choice to keep costs down is to simply render over the existing render. This is only possible in situations where the original rendering is in good condition and shows no sign of failure.
If you apply new rendering without assessing the existing structure, you run the risk of having both the new and old layers of render falling off, leading to health and safety issues, as well as added costs for repair. If you have minor issues such as cracks, your contractor will need to repair these before starting work on your polymer render, with small patch repairs usually costing between £100 to £350, depending on your type of render.
This method is far more time-efficient than a full removal of old render and can help trim down labour charges as well as hire charges for additional equipment. Render applications can start at £3,000 for small properties and rise to £6,000 and above for larger homes and even more for premium materials.
Instead of polymer, you can opt for cheaper alternatives if choosing a particular colour isn’t a big deal to you, or if you don’t need added benefits such as temperature adaptability as seen in plastic-bearing renders. Lime render costs around £20 per m2, while cement render is cheaper still at £10 per m2 - compared to the cost of polymer render, which is around £30 per m2.
Clad Over Existing Render
Another option to avoid the removal of the old rendering is to install cladding over your rendering. Like before, this is subject to your existing render being in good condition.

Cladding installation can cost around £3,800 and will take anywhere from two to three days, making it more time-efficient than removal of the existing render. The material you choose for your cladding - timber, UPVC or aluminium - will give you lower or higher costs, with timber being the cheapest and aluminium being the most expensive option.
Paint Over Existing Render
Our final option for homeowners with existing rendering in good condition is to paint your house over the existing render. If the full removal of the render isn’t necessary, this can be a great way of giving your home’s exterior a new lease of life while being budget-friendly.
Your contractor must assess your property’s render for any defects, and fix any problems before painting to both preserve the structural integrity of the existing rendering, as well as ensuring the paint finish is as seamless as possible.
Prices for masonry paint vary, but you can find 5-litre tubs for around £15, giving you a cost range of between £10 to £25 per m2 - which equates to £800 to £2,000 for supply costs only for a two-bed semi-detached house. You will then need to add on equipment costs, such as scaffolding, as well as factoring in your labourer’s day rate.
Removing Existing Rendering
If your home’s rendering is in a state of disrepair, you will need it to be removed before any work can start on replacing it. Some defects are too far gone to repair, such as when large areas of the surface have fallen away, and opting to repair these instead of replacing them can be a costly mistake.
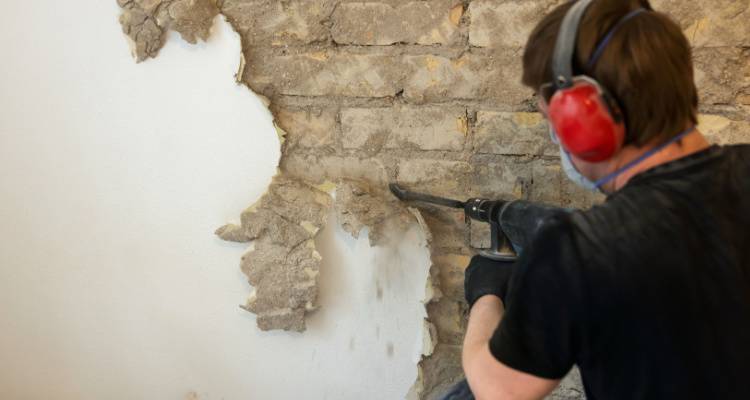
A common job for contractors concerns the removal of pebbledash render. This can cost anywhere between £2,100 to £7,800 and up, depending on your house size.
You may have already had your rendering removed - and for instances where it was pebbledash, you will need to assess your property’s substrate for damages during the removal. Issues with this layer cannot be ignored, and a fix is required before the new render or cladding is added, as failure to do so can negatively impact your home’s thermal efficiency.
Different Types of Render
You can also choose a different type of render, including:
Hiring Contractors Checklist for Polymer Rendering
Let’s take a look at the main considerations when hiring a contractor to carry out your home’s polymer rendering.
Verify Qualifications and Licences
When you start to gather your project costs from contractors, you must take into consideration their certifications and licences to ensure they are qualified. While there isn’t a set educational route to take to be adept in external rendering, general skills in plastering and rendering, construction and handling hazardous materials can indicate a skilled trader.
Be sure to check that the contractor has valid liability insurance in place, as this will keep both you and them covered in the event of any accidents during the project. If a trader doesn’t have insurance but ensures you that it’s fine, make sure that you avoid working with them, as that can be a strong indicator that the contractor isn’t professional.
Check Past Work History
Look at the contractor’s work history, paying close attention to the type of reviews they receive from their customers. If repeated issues with timekeeping, cleanliness and general work ethic are flagged, it’s best to continue your search until you find someone more respected in their field.
With a specialised job like monocouche rendering, make sure the contractor has experience in this exact area, and take a look at any photos or videos of their completed work to give you an idea of the type of finish you can expect.
Gather Several Quotes
While it’s a time-consuming job, it’s paramount that you collect several quotes for your job. This will help you to see the spread in project fees and allow you to see what’s a fair price and what is over- or under-priced.
Ask Questions
Don’t be afraid to ask any questions you may have. This will help you to see what sort of communication you might have with the trader, as well as find out about any potential hidden costs.
FAQs
What Is Polymer Render?
Can You Paint Polymer Rendering?
Is Polymer Render Better Than Other Types Of External Render?
Can I Repair My Home’s Polymer Render?
Is Polymer Render Attractive To Prospective House Buyers?
Sources
https://rapidrenderingbrisbane.com.au/polymer-rendering-blog
https://www.fmb.org.uk/resource/house-render-what-you-need-to-know-before-you-start.html